Making a better world with trust and creativity
Nikon, guided by its corporate philosophy of trust and creativity, continues to push the boundaries of human potential and work towards a sustainable society. With over 100 years of history, it leverages its expertise in applied optics and precision technologies to develop innovative solutions, aiming to contribute to a future where humans and machines co-create seamlessly.
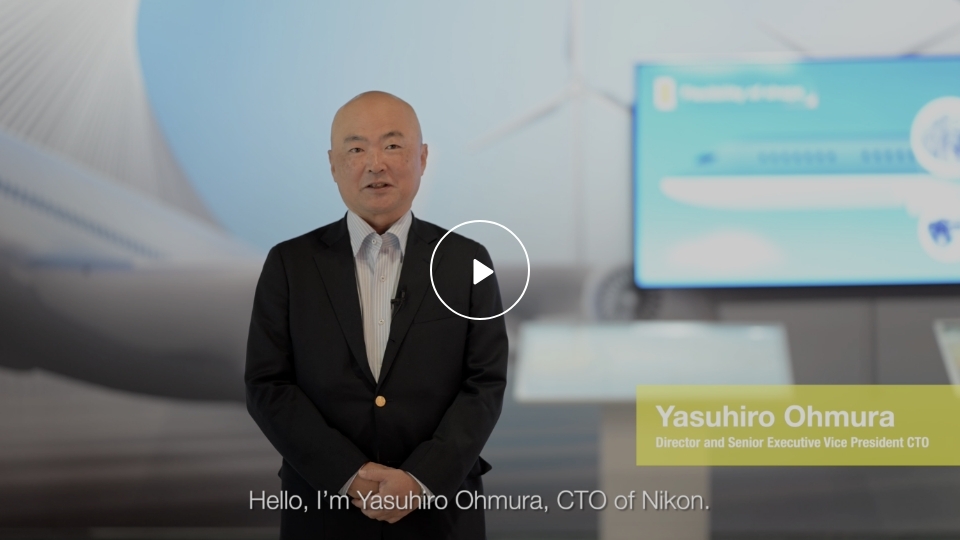
A message from Nikon's CTO
(2:53)Introducing Nikon's vision for the future through the products, services, and initiatives showcased at the event.
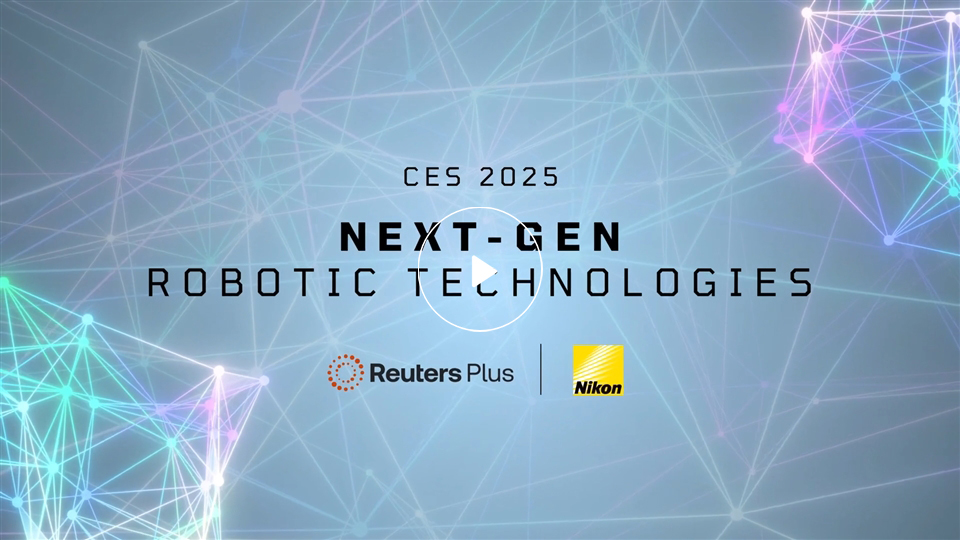
Reuters Plus Report Movie
(04:20)A report from a journalist at Reuters, the international multimedia news agency, highlighting the Nikon booth.
Please take a look at the Nikon booth at CES 2025.
Introducing Nikon's solutions that provide new value in a society where humans
and machines co-create seamlessly.
Robot Vision System/
Intelligent Actuator Unit
The future of robotics driven by
cutting-edge technologies
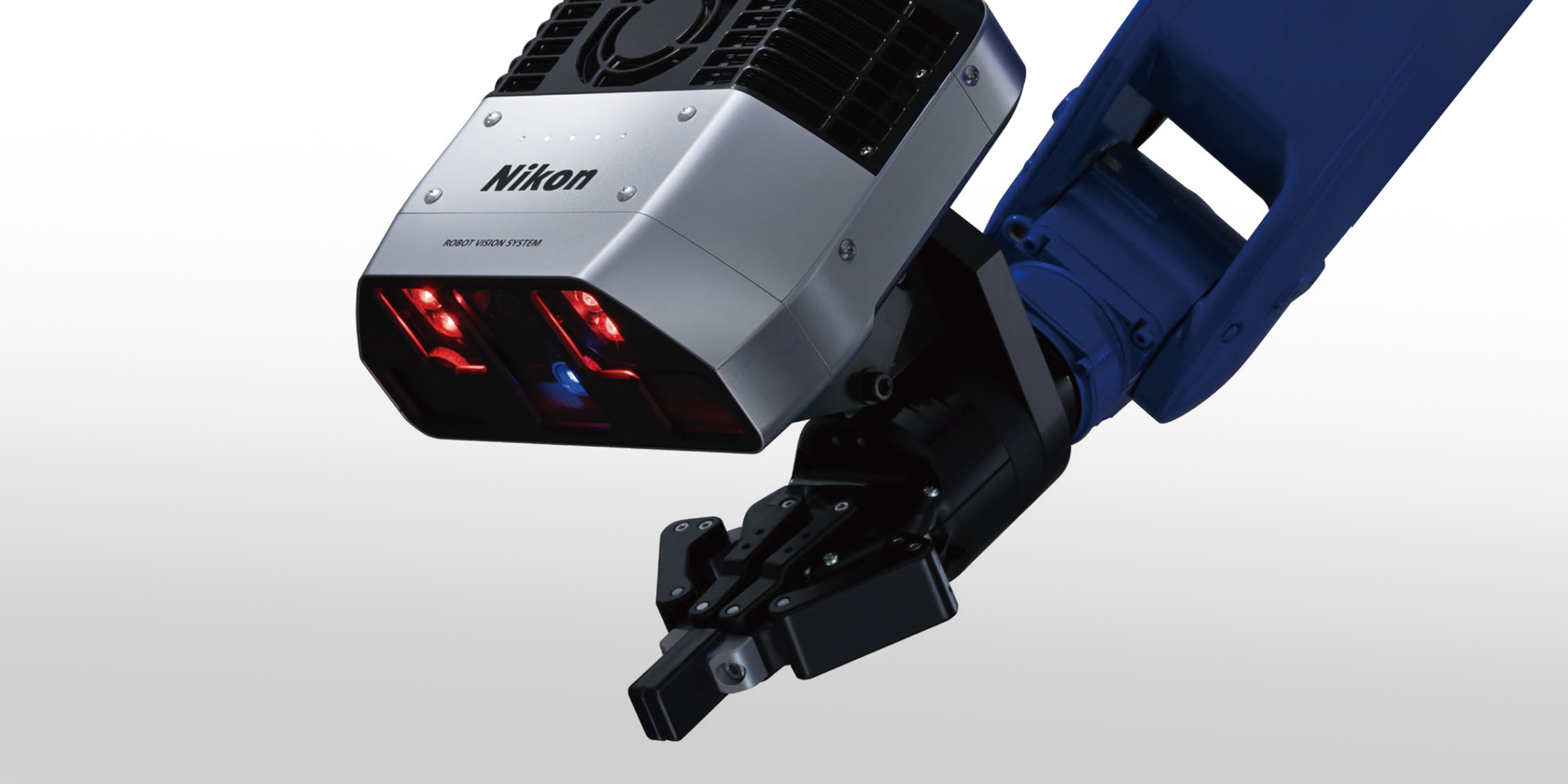
Nikon's robot vision system enables extremely fast, precise, and flexible robot movements that set it apart from the rest. By incorporating high-speed sensing — several times faster than the human eye — through 2D/3D cameras mounted on a robot's fingertips, Nikon's system enables exceptionally fast and flexible movements. This allows for the quick picking of randomly piled workpieces and also performing assembly tasks on moving workpieces. This system also designed to significantly reduces the teaching time, boosting both efficiency and flexibility for user.
Additionally, the C3 eMotion intelligent actuator unit for robotic joints was developed to allow any engineer to easily create human-collaborative robots without specialized knowledge.
At CES 2025, we will showcase the combined value of the robot vision system and intelligent actuator unit, brought to life under the theme of "The Restaurant of the Future."
Nikon is committed to advancing robotics, expanding the possibilities of manufacturing, and contributing to the creation of a sustainable industrial future.
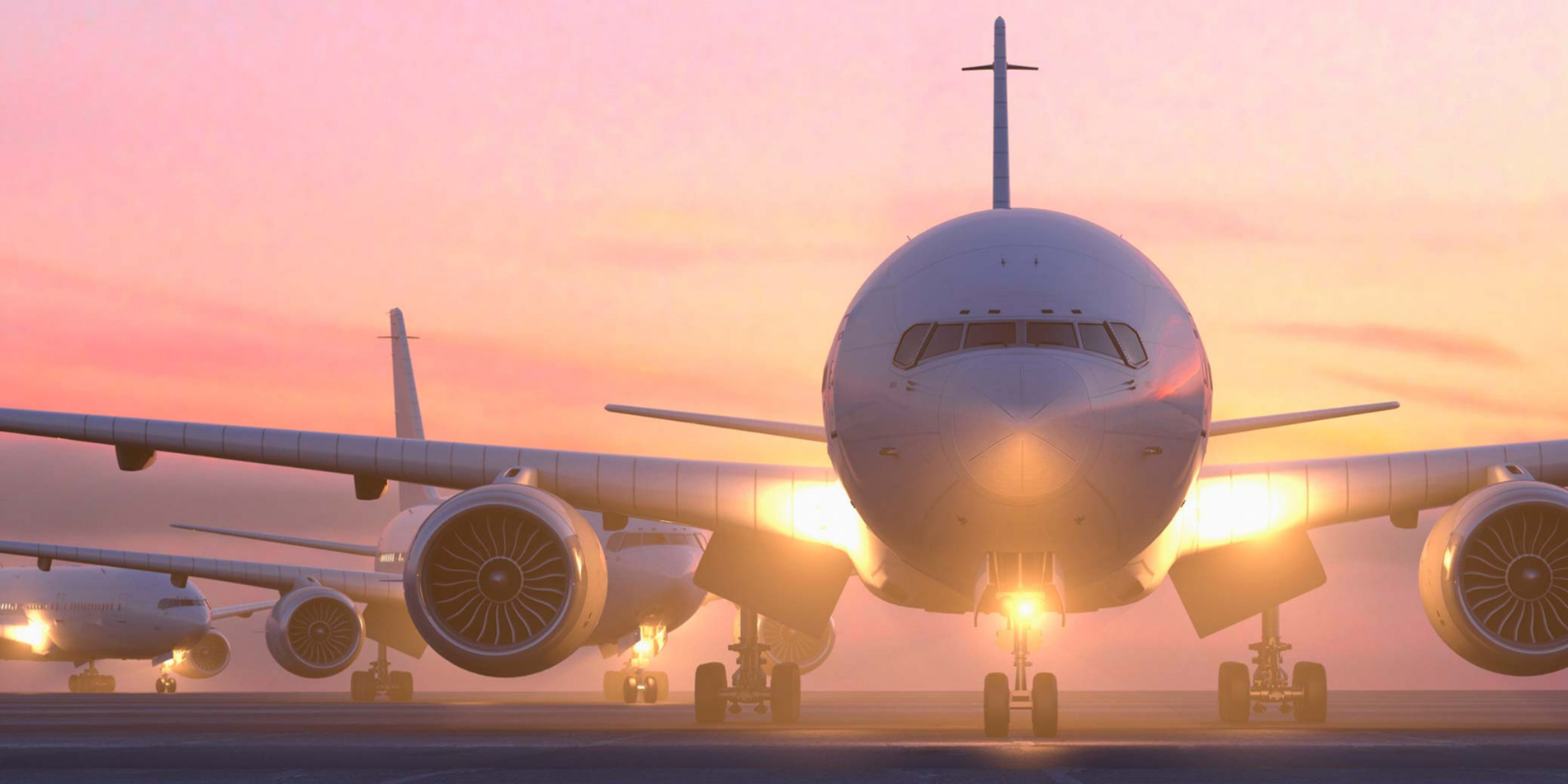
Riblet Processing
Nikon's shark skin-inspired
technology reduces energy loss
across industries
Nikon has leveraged its proprietary laser-processing technology to artificially apply riblets, artificial microstructures that resemble shark skin, to the surfaces of various product components. This technology enhances energy efficiency, and the development of Nikon's riblet-processing technology is currently being tested for practical use in wind power and aviation, with expectations for its contributions across a variety of fields in the future.
At CES 2025, Nikon will introduce this riblet-processing technology, highlighting its value from a biomimetics perspective—creating new technologies and products by mimicking outstanding characteristics found in nature.
Nikon provides innovative solutions to fully realize the value and potential of digital manufacturing.
In-Vehicle Camera
System
Aiming to create value across diverse fields with an innovative in-vehicle camera system

Advanced driver-assistance systems (ADAS*) and autonomous driving technology in the automotive industry are evolving every day. In addition, there is growing demand for methods to enhance visibility to prevent serious accidents caused by drivers not noticing signs or pedestrians. Nikon and Mitsubishi Fuso have developed an innovative in-vehicle camera system to create new value for future trucks and buses.
At CES 2025, we will showcase an immersive experience using VR technology. Nikon has developed an innovative camera featuring a single-lens system, which integrates telephoto and wide-angle functions to enable users to see far away and also check their periphery. We are exploring a variety of possibilities to expand the use of this innovative technology not only in vehicles but also in other diverse fields.
- *Advanced Driver-Assistance Systems: A general term for technologies that enable vehicles themselves to collect information on their surroundings, alert drivers and assist in vehicle control to ensure driver safety and comfortable driving.
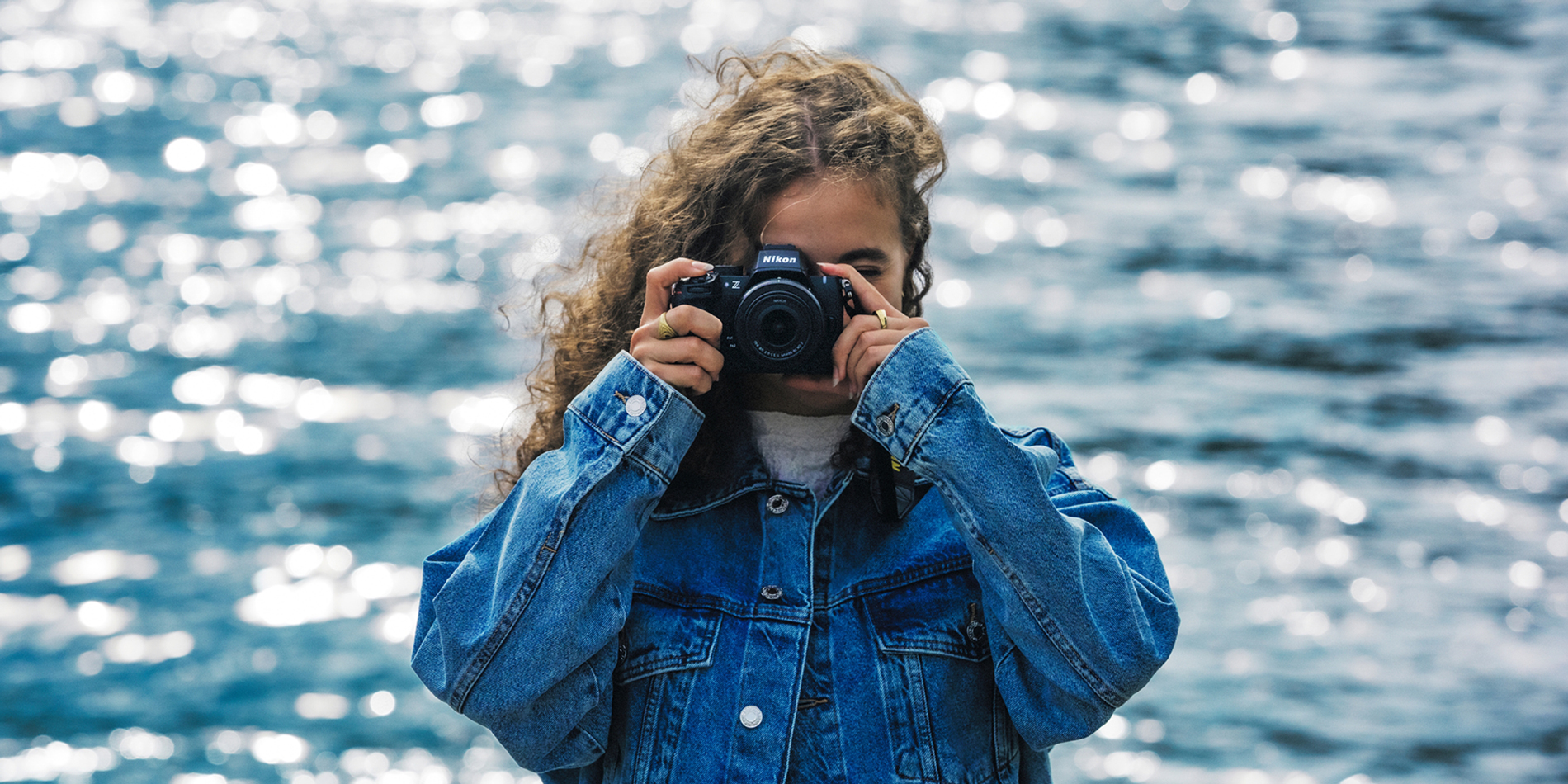
Mirrorless Cameras
Transforming visual storytelling
and unlocking creativity for all
users
The Z9 camera continues to push the boundaries of imaging expression, including video, thanks to ongoing firmware upgrades since its release.
The versatile Z50II strikes the perfect balance, offering creative options for custom looks and colors, alongside advanced features and performances inherited from higher-end models.
Together, Nikon's Z series cameras inspire originality and empower users to explore their own unique style of creations.
Paired with NIKKOR Z lenses, designed with a large-diameter mount and short flange distance to realize greater flexibility in optical design, the system delivers stunning resolution and beautifully natural bokeh, achieving remarkable imaging performance that never fails to amaze.
At CES 2025, in addition to viewing the newest products in the Z Series, visitors will be able to have their portraits taken by a professional photographer.
Supporting everyone in expressing their individuality, Nikon is shaping the future of visual storytelling.
The Artemis Mission
—Mirrorless Goes to the Moon—
The Artemis Mission
—Mirrorless Goes to the
Moon—
A historic collaboration capturing a world beyond imagination in extreme environments
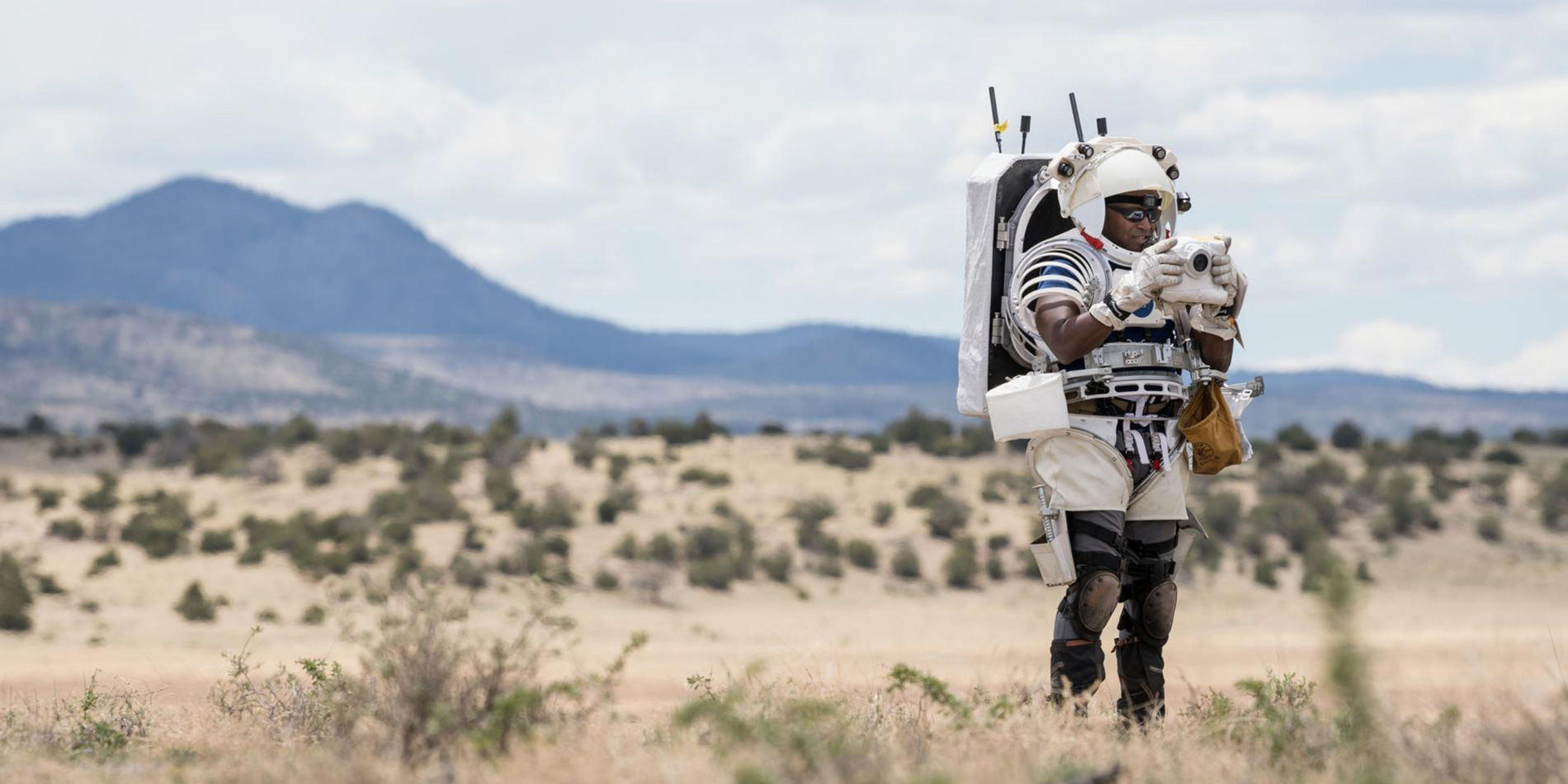
Credits: NASA / Josh Valcarcel
Nikon Inc., a subsidiary of Nikon Corporation, has entered into a Space Act Agreement with NASA to support the development of the Handheld Universal Lunar Camera (HULC) for the upcoming Artemis mission, which aims for a crewed lunar exploration in mid 2027. As part of the mission, named Artemis III, NASA plans to utilize a modified version of the mirrorless Z9 camera for the lunar landing phase, and it is expected to be used by the astronauts while on the Moon's surface.
At CES 2025, Nikon will showcase its solutions that support this monumental project, including the thermal blankets designed to protect the camera and lenses from lunar dust and extreme temperature changes.
Through its imaging technology, Nikon is delivering historic moments to the world.
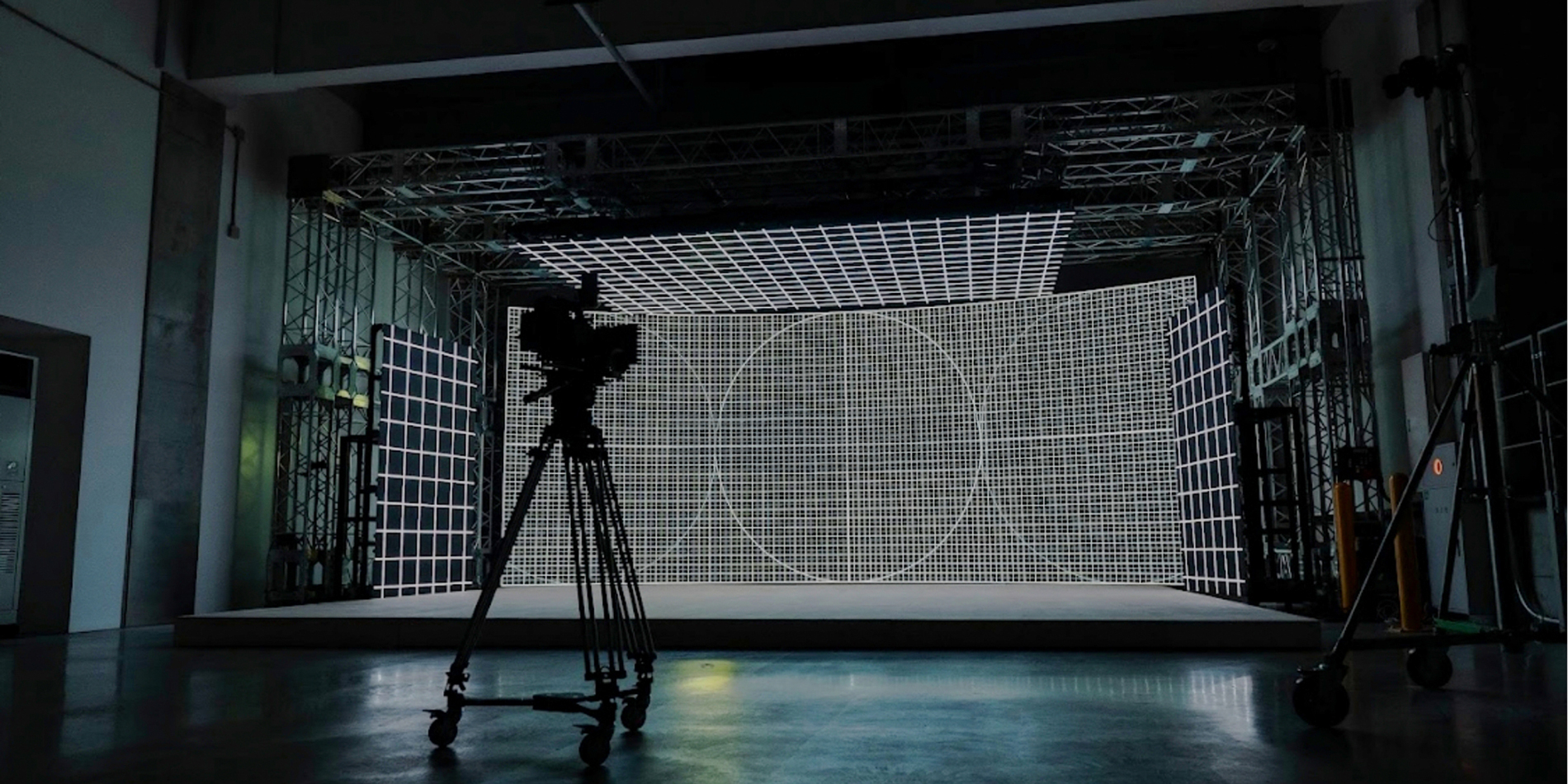
Virtual Production
Bringing innovation to the
world of video through
revolutionary visual solutions
Virtual Production displays high-definition 3D imagery on large LED screens, allowing performers and objects to be filmed from any angle. By eliminating the need for compositing, it paves the way for groundbreaking visual expressions. Employing Nikon's advanced imaging technology, alongside the expertise of MRMC — which became part of the Nikon Group in 2019, and specializes in broadcast camera robotics and virtual production — and RED, the pioneer in professional cinema cameras, which joined the Nikon Group in 2024, video production reaches new heights. This technology allows filming against any backdrop, regardless of time or location.
At CES 2025, MRMC's StudioBot LT and RED's cinema KOMODO X camera will be showcased, offering attendees the opportunity to experience an immersive activation provided by virtual production experts Disguise. The activation will simulate a broadcast, where the visitor can take on the role of a weather forecaster. At the same booth, Nikon Creates, part of the Nikon Group, will showcase immersive footage filmed using drones and LED virtual production. This captivating content will be screened on a massive 9.5m x 3.0m screen at the entrance of the Nikon booth. Nikon is committed to supporting a society where people can connect across time and space
through the power of video production.