Reducing CO2 emissions from lens manufacturing process through technology
highlight
Nikon has set the goal of reducing its CO2 emissions by 26% by 2030 compared with the FY2013 level. Together with energy conservation measures at office buildings and other initiatives, Nikon is leveraging its advanced technological capabilities to cut CO2 emissions in line with this target.
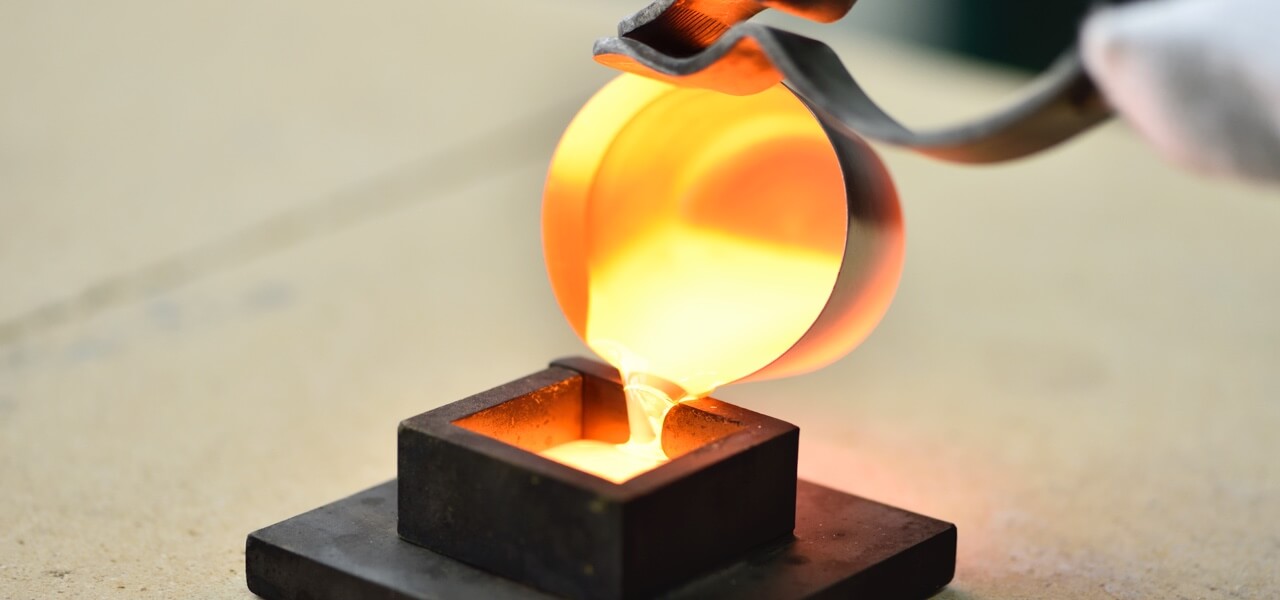
Making up a quarter of the Group’s CO2 emissions, lens manufacturing operations are the key to reducing total emissions
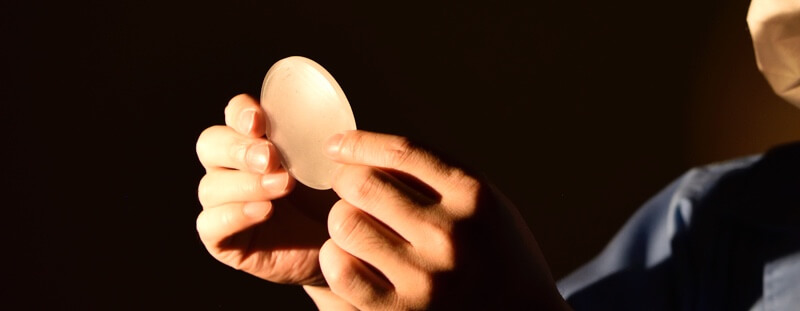
Nikon’s high-quality lenses can be found in a wide array of products, including cameras, microscopes, medical devices, industrial equipment, and even space-related equipment. However, the manufacturing processes necessary to produce these lenses consume a vast amount of energy. In fact, the amount of energy used to manufacture lenses from optical glass accounts for about a quarter of the Nikon Group’s total CO2 emissions. Nikon has been working hard to reduce the environmental impact of its lens manufacturing operations through a broad range of initiatives and measures. A few of them are described below.
CO2 emission ratio of Lens Manufacturing within the Nikon Group
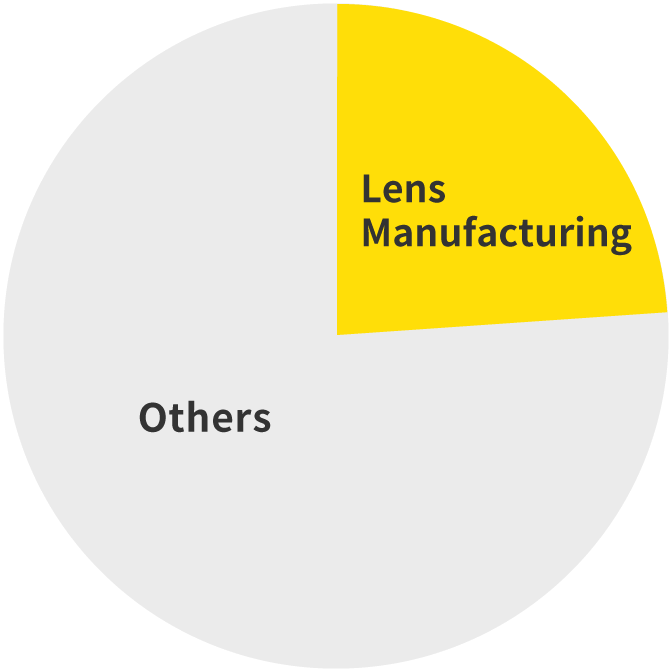
Case Study.01Using simulations to dramatically reduce the number of prototypes.
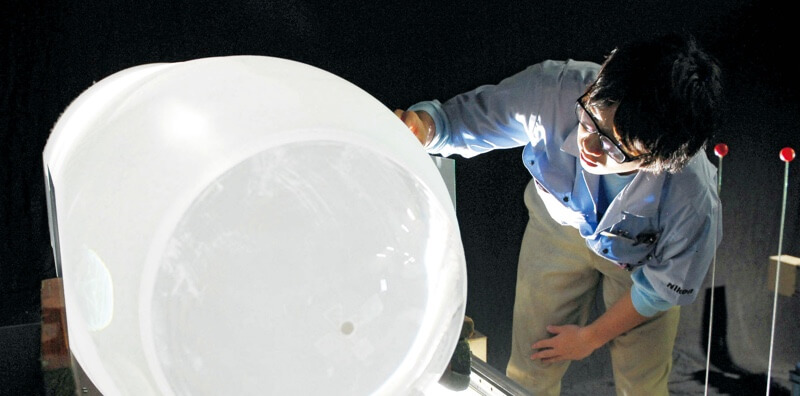
Semiconductors are essential for all kinds of products today such as smartphones, while flat-panel displays (FPDs) are ubiquitous in televisions and digital signage. Nikon semiconductor and FPD lithography systems are widely used in the manufacture of these products. The lenses used in these ultra-precise exposure systems are made of synthetic silica glass.
Synthetic silica glass is made by melting raw materials at high temperatures for an extended period to produce a chemical reaction, and then forming the glass into a large rod-shaped piece called an ingot. This process requires a substantial amount of thermal energy even to produce a single ingot as a prototype. As an alternative to making physical prototypes, Nikon has developed a simulation system for testing prototypes under virtual conditions. Developing the system presented many challenges because simulations must take into account a combination of many factors, including fluid dynamics and chemical reactions. Nikon successfully overcame the challenges by applying technological expertise and experience built up over many years. Using simulations, Nikon has been able to cut energy consumption by about 52,000 kilowatt hours - equivalent to 26.3 tons of CO2 emissions - which would otherwise have been required to make physical prototypes using one kind of heating furnace.
Nikon is using similar simulations to achieve efficiency improvements in the test production of fluorite. It takes a vast amount of power to create the high-purity, low-defect fluorite used in semiconductor exposure equipment and everyday cameras due to the long period of heating in an heating furnace. Nikon estimates an approximate 15 tons annually reduction in CO2 using virtual simulations compared with making physical prototypes.
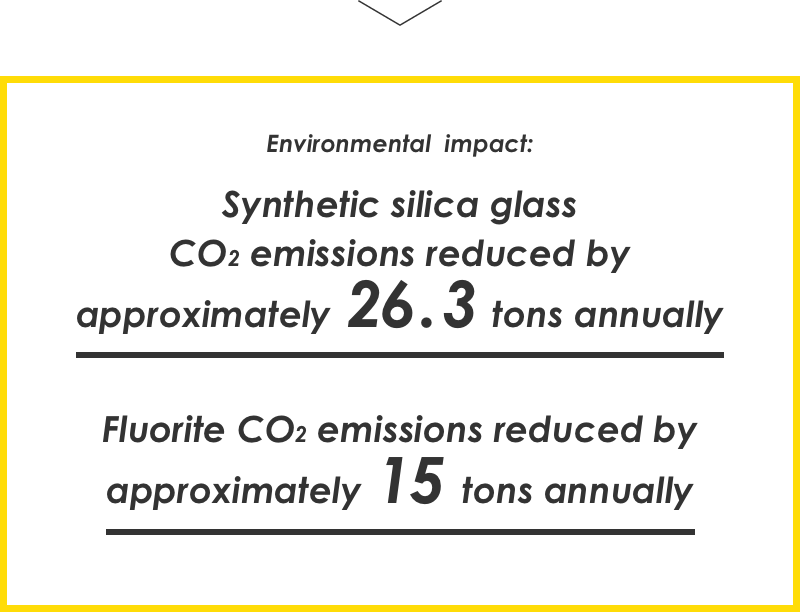
Case Study.02Improving optical glass testing efficiency to reduce time from development to stable mass production by two-thirds
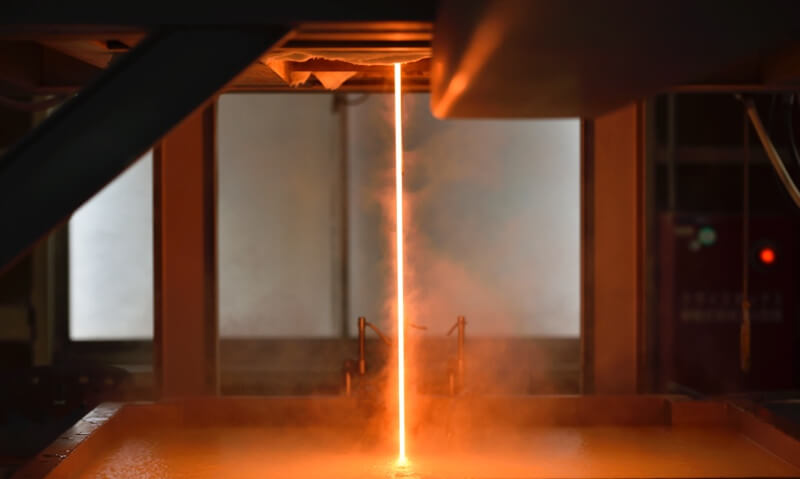
Optical glass is used in a variety of products such as cameras and microscopes. When developing these lenses, small-scale tests of the optical glass must be performed to calibrate manufacturing parameters, and then large-scale tests to verify the feasibility of mass production. During the large-scale tests, uneven temperatures may occur inside the production equipment, requiring the process to be repeated from the small-scale test stage. This not only takes time and energy, but also generates a large amount of glass waste.
In response to this problem, Nikon drew on its expertise in quality engineering to develop a method that enables small-scale test results to be consistently replicated in large-scale tests. Applying this method has brought the time from product development stage to mass production down to less than a year - a third of what it was before. Electricity consumption has also been cut by 170.7 MWh (97.5 tons of CO2 equivalent) and glass waste reduced by 15.6 tons (228.7 tons of CO2 equivalent) compared with the previous fiscal year. As an added benefit, the new method has greatly reduced the number of product defects during mass production, further reducing glass waste by about 7.0 tons annually (102.9 tons of CO2 equivalent).
Nikon has applied technical knowledge obtained from quality engineering experiments to the melting process used in mass production. This has resulted in improvements to the melting process and a reduction in power consumption when mass producing newly developed optical glass. Applying this process to other similar types of optical glass (10 types as of 2018) has led to a reduction in power consumption of 106.2 MWh (55.3 tons of CO2 equivalent).
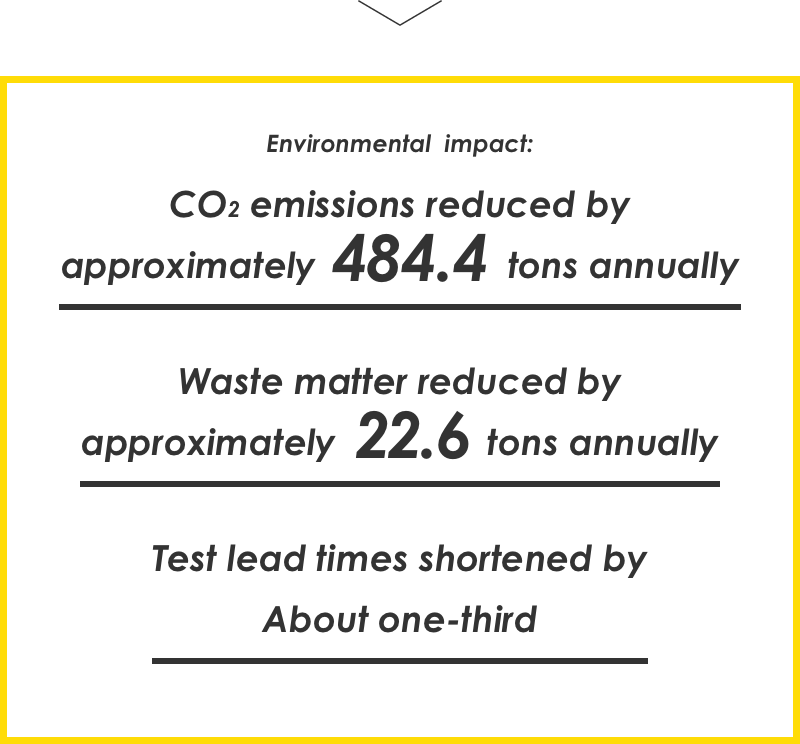
Case Study.03Reducing waste glass by improving the precision of lens pressing processes
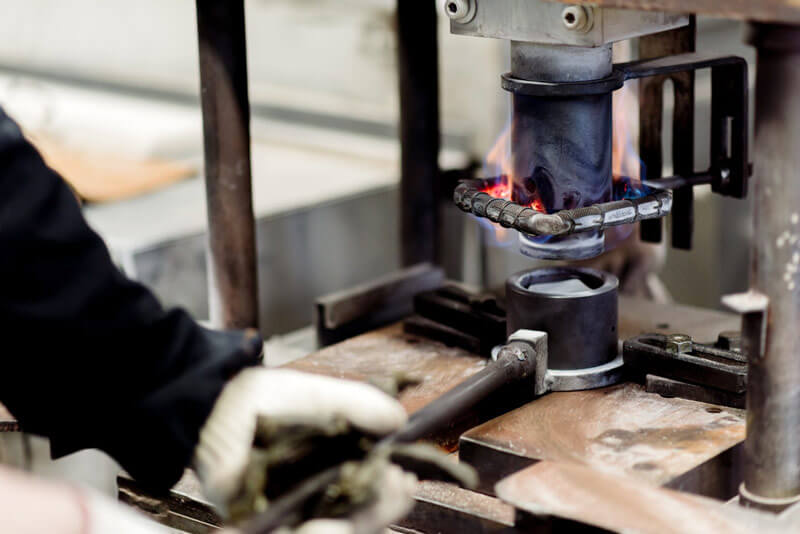
To manufacture the lenses we find in so many products today, spherical lenses are initially pressed from square pieces of glass using metallic molds, and then ground and polished. This pressing process involves countless combinations of glass materials and mold shapes, which are determined by skilled and experienced workers. As a result, the shapes of pressed lenses are slightly inconsistent, so they are made slightly larger to provide extra grinding allowance. However, this also results in a large amount of ground glass being generated as waste in the lens manufacturing process.
To solve the problem, Nikon looked at each step of its pressing process and improved each one to reduce waste as much as possible. These improvements effectively decreased lens shape variation by about 40% and reduced the amount of glass material per lens by 10%. After extending this initiative to the production of 16 lens products, Nikon succeeded in reducing glass waste by 2.5 tons annually (approximately 36.8 tons of CO2 equivalent).
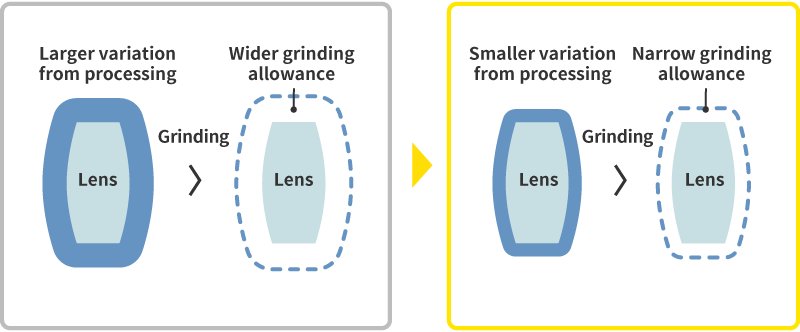
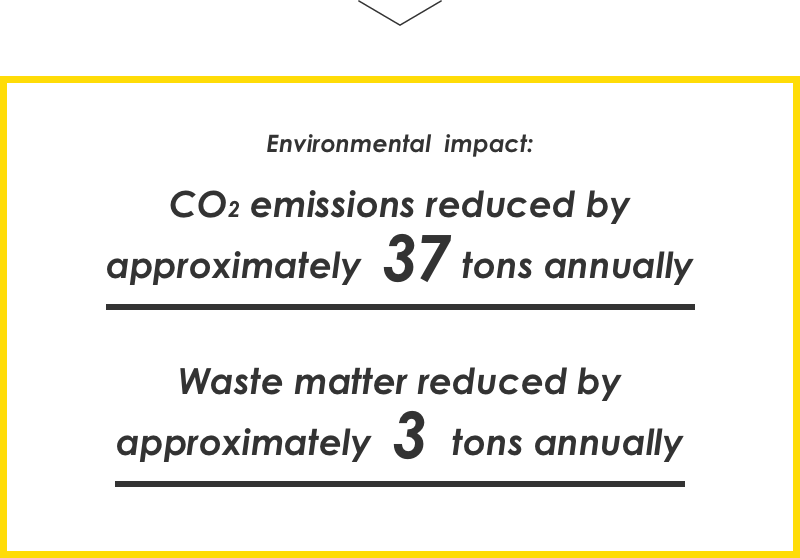
OutlookReducing environmental impact while continuing to produce high-performance, high-quality products
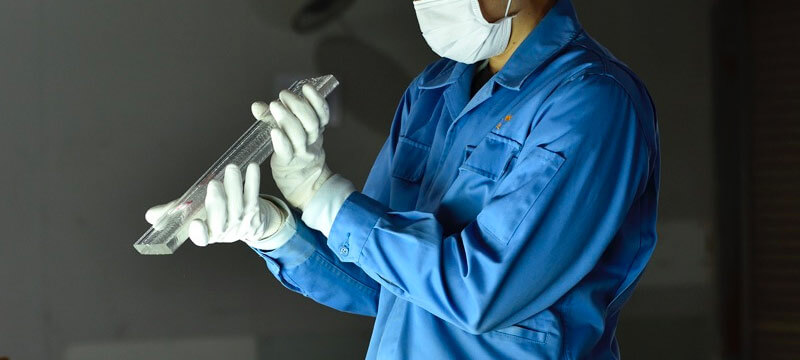
Nikon recognizes that initiatives like those described above can continue and be expanded to include a wider range of products and manufacturing processes. The company regularly holds group-wide conferences to share information on outstanding new technologies and ideas that have come from each workplace, thereby enhancing the technological capabilities of the Group as a whole. Looking ahead, Nikon will continue to pursue the highest product quality while working to reduce its impact on the environment.
Related SDGs
SDGs: Sustainable Development Goals
In 2015, the international community adopted a set of targets for sustainable development, to be achieved by 2030. The 17 global goals address issues such as poverty, hunger, education and climate change.
Related information
- Environmental Management
We introduce the Nikon Long-term Environmental Vision and environmental activities taken by the Nikon Group.
Highlight
- The Power of Imaging: Bridging Space and Earth
- Exploring possibilities for imaging expression with the creators of tomorrow
- Riblet Processing — A Technological Innovation for Aircraft Leading Toward Achieving Carbon Neutrality
- Reusing semiconductor lithography systems to reduce waste
- Supporting children’s education in Laos
- Providing solutions for iPS cell-based drug discovery
- Reducing CO2 emissions from lens manufacturing process through technology
- Product Manufacturing and Social Contributions through Sharing Our Vision with Procurement Partners
- Fostering “Image Culture” through the Nikon Photo Contest A Conversation with those Inspired by Photography
- Worldwide employee training: ensuring Nikon remains a company that people trust
- Superior quality born from a collaborative production process